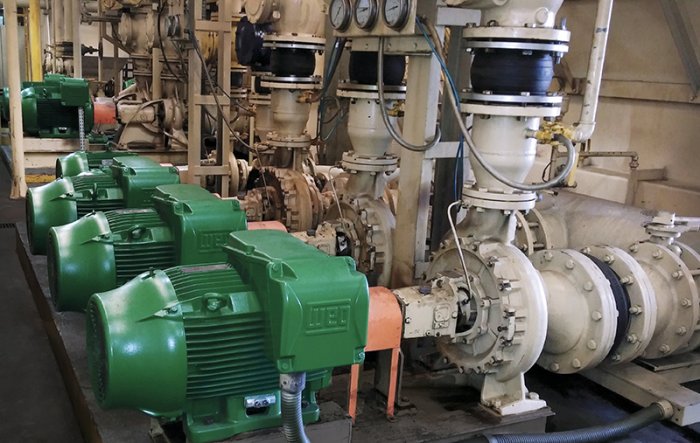
Investing in energy efficiency is a requirement that many companies have found important in lowering costs and increasing market competitiveness. The high energy rates in Brazil have led companies to seek alternatives in reducing electricity consumption, optimizing processes and reducing costs. According to data provided by Eletrobras, 42% of electrical usage in Brazil is attributed to industry with electric motors contributing 70% of this consumption.
In order to reduce energy consumption, Embraco, a global company and world leader in the hermetic compressor market for refrigeration, consulted with WEG to audit and analyze their energy usage at the Joinville City compressor plant. WEG determined that an area where they could reduce energy consumption and increase efficiency was in their line of machining units. Mr. Ricardo Samistraro, an expert in electrical processes and leader of Embraco’s Energy Pilar explains what led them to contact WEG: “Besides being a world leader in products with high energy efficiency indexes, WEG has a team of application engineers with great energy experience, which helps identify opportunities, energy losses and provides support during the project implementation phases.”
With the energy audit made by WEG, It was possible to identify that the electric motors, responsible for pumping oil to the milling machines, consumed much more energy than necessary for the application. This analysis indicated a potential energy consumption reduction of approximately 30% with the use of WEG products.
Through the exchange of information between the technical staff of WEG and Embraco, the solution resulted in the replacement of the existing pump motors with new WEG motors. The new system used high efficiency W22 IR3 Premium and W22 IR4 Super Premium motors driven by CFW700 and CFW11 frequency inverters, integrated with a pressure transducer. These WEG motors lines have efficiency levels above that required by Brazilian law for Energy Efficiency, contributing to considerable energy savings and a more rational use of natural resources.
The project also encompassed greater control of the oil distribution system flow rate, which previously was carried out through manual valves. Since the work demand of the milling machines is variable the manual valve system was causing an unstable pressure in the system and unnecessary power consumption. With the new optimized system, the pressure became stable and the energy consumption proportional to the production rate.
According to Mr. Ricardo Samistraro, “The replacement of the existing motors with WEG high-efficiency models coupled with the new automation system, not only reduced energy consumption, but also has provided 47% savings, equivalent to 2,227,286 kWh / year, approximately half of which was consumed previously in the oil plants. An additional benefit was achieved in terms of competitiveness, by being able to produce the same number of compressors using less energy.” Samistraro also stated “That by using a WEG technological solution we obtained significant energy savings and a high reliability of operation."