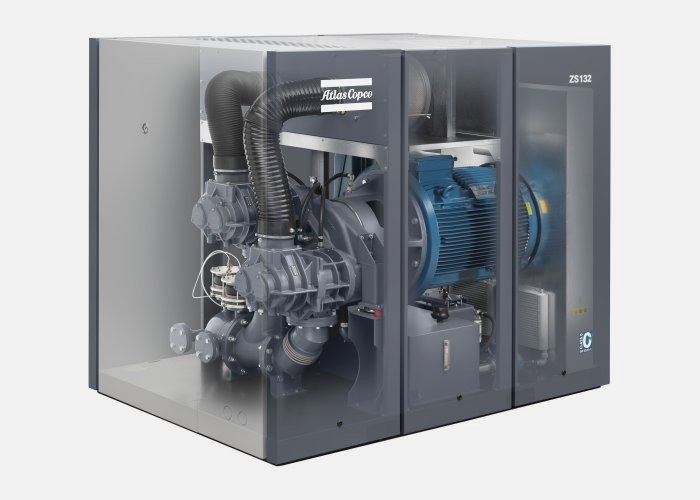
Blowers, which produce large volumes of air at relatively low pressures – typically from 1 to 4 bar – are a significant consumer of energy in many industrial processes. In wastewater treatment for example, they are used to deliver air to the aerobic bacteria that play a central role in breaking down contaminants. Air blowers consume up to 70% of the energy used in wastewater treatment, which in turn accounts for around 3% of total energy consumption in industrialised countries. The Atlas Copco ZS blower range has been designed to transform energy efficiency in these applications, using a range of improvements that reduce energy consumption by more than 30% compared to traditional designs.
As water utilities and industrial users increasingly look for ways to reduce energy use, there is considerable interest in improving blower efficiency. The ZS units replace the classic roots compressor design, traditionally used in low-pressure air applications, with a screw compression element. This greatly increases the efficiency of the blower, and maintains better efficiency across a wider range of operating speeds. To minimise overall energy consumption, Atlas Copco has made a number of other design refinements in the ZS range, including careful management of airflows through the blower and the selection of highly efficient power and transmission components.
The WEG W22 three-phase motors chosen by Atlas Copco to power the ZS Blowers, have been designed specifically to meet the requirements of the most demanding industrial users, including reduced energy consumption, increased productivity, extended lifetime and lower maintenance. The frame and cooling system of the motor have been optimised to deliver better airflow to its internal components, for example, improving operating efficiency even in tough environmental conditions. Special bearing seals also extend the lifetime of the motor in aggressive environments by protecting it against the ingress of water and dust.
These features allowed WEG to ensure that it could provide motors capable of meeting both its customer's efficiency specifications and its requirement for a component life of 40,000 hours, with re-greasing intervals of 4,000 hours. The motors must be able to deliver this level of reliability even in extremely tough environments, like 24/7 running in plants located in tropical regions where ambient temperatures can be as high as 46°C.
“Not only do we offer truly global supply and support, but also outstanding quality - all our motors undergo extensive testing regimes, both in the lab and the field,” says Michel Dandoy, Key Account Manager at WEG Benelux. “That, together with the fact that we manufacture all the key components in-house, helps give customers like Atlas Copco the confidence that we can meet their demanding quality requirements. We also certify our products to a broad range of international standards, which simplifies global supply.
“The W22 range is available in both IE2 and IE3 energy efficiency ratings as standard, which very few other electric motors are; combined with a matched CFW11 inverter drive we are able to deliver huge energy savings from what, to us, is a standard product, with all the support and availability you would expect. We also offer the W22X series of motors available in Ex-n, Ex-e and Ex-d configurations for hazardous areas, which, along with the standard W22 machines, are available in power ratings from 0.25kW right through to 4MW and efficiency classes IE2 & IE3”
WEG is one of the world’s largest and most successful manufacturers of electric motors, related control equipment and automation systems. Specialising in the manufacture and supply of energy efficient products for all industrial applications.
About WEG
A global major in the power distribution, automation and control sectors, WEG has just celebrated its 50th birthday. The company’s global sales now exceed the US$3-billion mark, representing increasing global success across a wide range of product groups, including the latest generation of transformers, LV control gear, generators, inverter drive systems, soft starters, LV and HV motors, ATEX- compliant explosion proof motors, smoke extraction motors and full turnkey systems. In addition, WEG has recently made a significant strategic expansion of its product portfolio, following the establishment of a joint venture for the manufacturing of wind turbines and the purchase of an Austrian gearbox manufacture, WATT Drive.