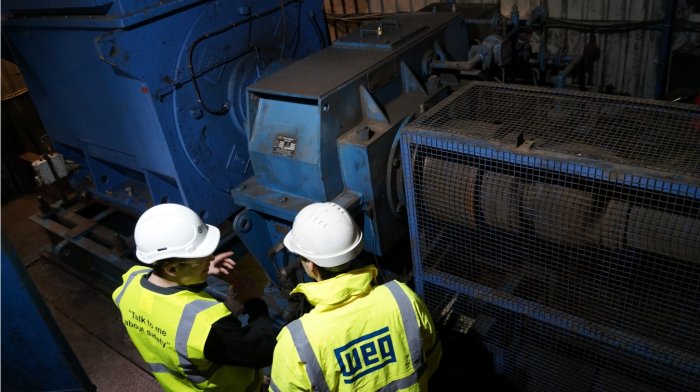
Designed to fit into the exact footprint of the legacy OEM equipment, the new 6.6kV, 3MW motor was the most cost effective option available for the giant shredder based in Newark Nottinghamshire that process over 1,000 tonnes of scrap per day.
The relationship between WEG and Sims Group Ltd. goes back several years when the first motor was installed at the company's Newport site. The performance and reliability of this project has seen a further ten high voltage WEG motors being installed by Sims. For the most recent installation in Nottingham, the requirement for a robust, reliable and efficient motor was important, but the principal demand was for a motor which would fit exactly into the footprint of the legacy motor, without any additional engineering.
The Nottingham site has the capacity to process up to 1,200 tonnes of scrap metal every day which arrives from a number of regular customers as well as members of the public. Sims provides a recycling service for End-of-Life Vehicles (ELVs), industrial scrap, domestic appliances as well as non-ferrous materials. All the received material is fed into the shredder by an inclined conveyor where it is literally torn to pieces by the rapidly-spinning hammers. The resulting fragments are then sorted into different categories with the ferrous material being sold back to the metals industry.
Site engineers from WEG visited the installation to discuss the list of requirements and to record all the necessary measurements for the design team. With considerable experience in this application, the WEG engineers understood the demanding environment as well as the customer's expectations for reliability and efficiency.
Based on the WEG 'M' Line motor range, the casing for the 800 frame motor was designed so that the fixing points and the footprint of the new motor would exactly match those of the old motor. With the precise measurements for the drive shaft height and diameter, the installation time for the new motor would be minimised, allowing the Sims installation team to complete the testing and commissioning with a minimum of lost time.
Wayne Oscroft, Electrical Engineer for the Northern Region of Sims Metal Management comments: "We looked at a number of options for replacing the existing motor, including a new OEM unit and repairing the existing motor, but the most cost effective solution was presented by WEG. The key for us is maintaining our operational efficiency so, while cost is always a factor, we needed to minimise the downtime imposed by the motor change as well as ensuring that the new motor would provide excellent efficiency and reliability.
"Sims has worked with WEG on other projects in the past and that experience, combined with its reputation, has given us the confidence to place another order with them. The new motor was installed by our engineers without any problems and it has been performing at more than 96% efficiency, which is excellent for this size of motor."
All of the material that is generated by the shredder is carefully sorted before being sold to various customers. Most of the ferrous material is shipped through the rail head on site to a number of iron and steel works, both in the UK and abroad. In all, Sims exports roughly 2.5 million tonnes of metal every year, with around 60% going to South East Asia.
WEG's 'M' Line motor range is designed for larger applications in the output range up to 50MW and voltage range to 13,800V. Manufactured from robust cast iron or welded steel plate, the 'M' Line range of motors provide outstanding performance and high efficiency operation. Key to this performance is a design that delivers excellent structural strength and low levels of vibration and noise. The same design also provides the user with the flexibility for eight different methods of cooling to meet the constraints of individual applications.